SHELL & TUBE
Shell & Tube
Heat Exchanger.
A Shell and Tube is the most common type of heat exchanger used in applications that require higher pressures and temperatures. Consisting of a tube bundle inside a shell, this basic design is heavy duty, rugged and durable. The system is simple, two fluids of different temperatures are circulated through the heat exchanger. One fluid flows through the tubes while another fluid flows over the tubes providing an optimum and efficient heat transfer.
Advantages of a Shell & Tube
Application
Higher pressure and temperature options available
Design
Basic, heavy duty, rugged and durable
Lifespan
Average life is 15-20 years; however it is
not uncommon to be in service for over 30 years
Economical
Typically less expensive than other types of
heat exchangers including a plate and frame
Main Components of a Shell & Tube
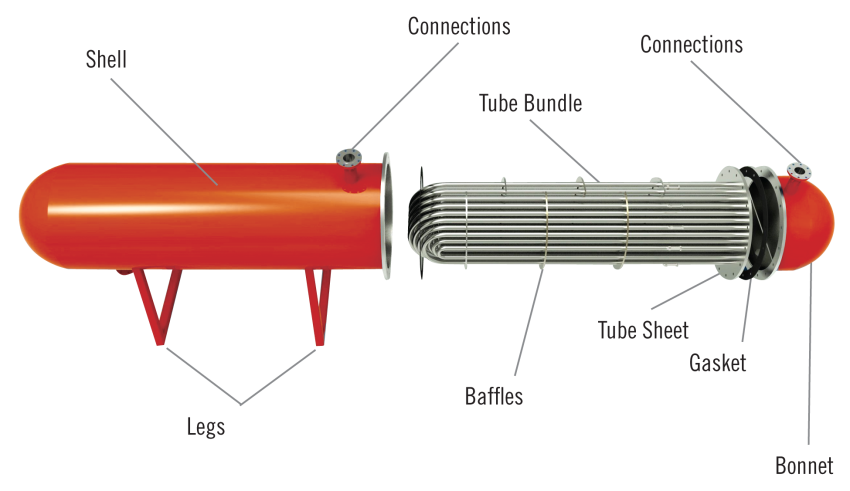
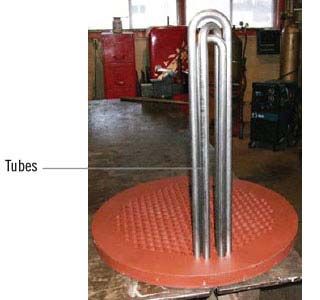
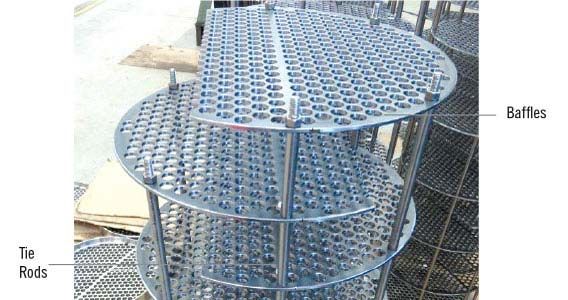
The tubes are typically copper or stainless steel with a ¾" or 5/8" outside diameter, while the remaining components are usually manufactured from milled steel.
Tie rods (circular metal rods) and spacers hold the tube bundle together while holding the baffles in the correct position. The tie rods are fastened into the tube sheet then secured at the farthest baffle. The number of tie rods, baffles and tubes depends on shell diameter and required application.
Applications (Shell & Tube)
Food & Beverage
(Breweries, Dairy, Fruit, Vegetable)
Pasteurization
Sterilization
Evaporation
UHT Treatment
Reception Thermization
Wort Boiling
Sterilization
Evaporation
UHT Treatment
Reception Thermization
Wort Boiling
Industrial
(Automotive, Mining, Pulp & Paper, Sugar)
Water Heating/Cooling
Demineralization
Evaporation
Economizing
Heat Recovery
Quench Oil Cooling
Caustic Solution Heating
Demineralization
Evaporation
Economizing
Heat Recovery
Quench Oil Cooling
Caustic Solution Heating
Energy
(Biofuels, Nuclear, Renewable Power, Oil & Gas)
Heat Recovery
Geothermal
Quench Coolers
Lubrication Oil Cooling
Corrosive Fluid Heating/Cooling
Crude Oil Heating
Diesel Engine Cooling
Auxiliary Cooling
Geothermal
Quench Coolers
Lubrication Oil Cooling
Corrosive Fluid Heating/Cooling
Crude Oil Heating
Diesel Engine Cooling
Auxiliary Cooling
Chemical & Pharmaceutical
(Fertilizers, Petrochemicals, Inorganic Chemicals)
Solvent Heating
Glycol Cooling
Reactor Cooling
Extraction
Fermentation
Fragmentation
Methanation
Glycol Cooling
Reactor Cooling
Extraction
Fermentation
Fragmentation
Methanation
Commercial HVAC
(Hospitals, Condominiums, Shopping Centers)
Domestic Water Heating
Swimming Pool Heating
Free Cooling
Cooling Tower Isolation
Heat Pump Systems
Heat Recovery
Thermal Storage Systems
Swimming Pool Heating
Free Cooling
Cooling Tower Isolation
Heat Pump Systems
Heat Recovery
Thermal Storage Systems
Marine
(Container Vessels, Bulk Carriers, Barges)
Lube Oil Cooling
Auxiliary Power Generation System
Jacket Water Cooling
Central Cooling
Seawater Isolation Exchanger
Engine Oil Cooling
Ventilation Coolers and Heaters
Auxiliary Power Generation System
Jacket Water Cooling
Central Cooling
Seawater Isolation Exchanger
Engine Oil Cooling
Ventilation Coolers and Heaters
Common Shell & Tube Heat Exchanger Designs
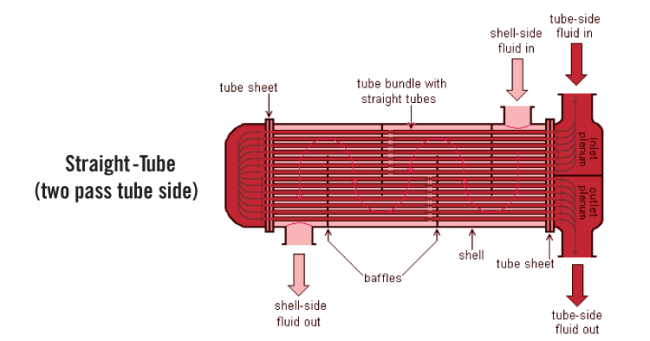
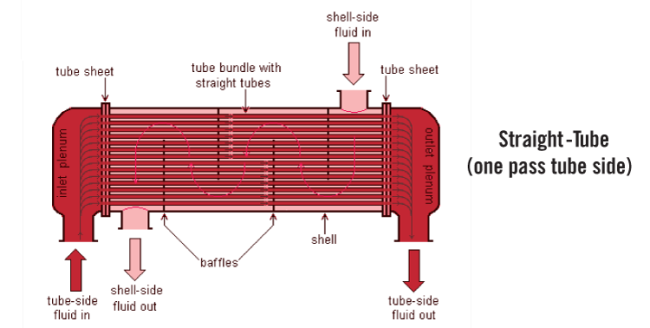
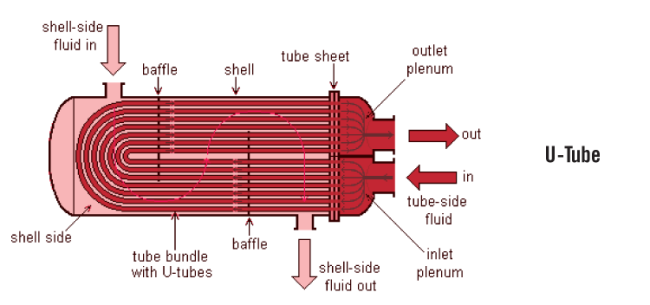
Potential Issues with a Shell & Tube Heat Exchanger
- When vacuum breakers or thermostatic vents are not installed or functional the tube can be sucked in and break.
- If the bundle is subjected to temperature extremes (thermal shock), the tubes will develop spiral cracks.
- On steam applications, harmonics can occur. This constant vibration can cause the steel baffles to eventually cut into the copper tubes.
- Chemical corrosion resulting from interaction between the heat exchanger and the circulated fluids.
- Marine film or coating on tubes such as scale, mud, algae and zebra mussels plugging tubes, this results in higher corrosion and restricts heat flow.
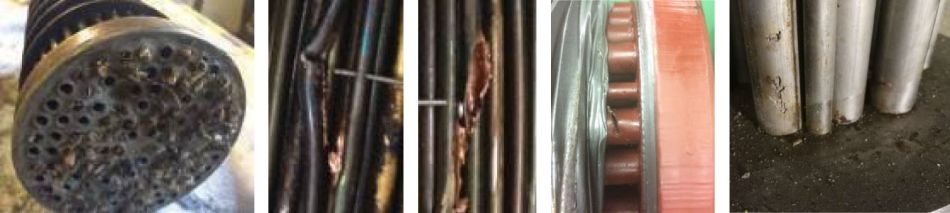